多くの製造業では「在庫削減」「リードタイム短縮」「納期遵守」「生産性向上」などの改善効果を期待して、生産スケジューラーの導入を検討しています。しかし、ソフトを導入するだけでこれらを達成できるものではなく、目的や運用方法をよく考える必要があります。
工場での計画作業の課題
これまでの経験から、よく耳にする課題として下記があります。
①Excelによる計画作成および変更作業に手間がかかる
飛び込み注文、数量や納期変更、作業者の欠勤や機械故障などによる計画更新が煩雑。
1つの作業変更に影響する他の作業を調整するのが大変。
②ベテラン計画担当者に依存している
計画作業のノウハウが特定の人に依存しており、引き継ぎができない。
③製造現場の作業実績が計画にフィードバックされていない
製造実績を踏まえて次回の計画を立案することができない。
これらに対して生産スケジューラーを活用して、計画立案作業をすばやく行います。
導入目的の明確化
上記の課題から「計画業務の標準化・効率化」を目的に始めることが多いのですが、追加要件として「納期回答をしたい」「資材発注に利用したい」などがあがります。それぞれを対応するには、業務フローの整理や追加データの準備などが発生するため、当初のスケジュールでの稼働が難しくなります。次ステップでの対応とするなどして、スモールスタートすることをお勧めします。運用を開始することで、追加要件が「本当に必要なことか」、また「運用できることか」を判断しやすくなります。
計画の対象
生産スケジューラー上で、工場の全ての工程および全ての機械設備や作業者を登録しようとされるユーザー様がいます。しかし、工場を再現することが目的ではないと思います。多くの場合、重要な工程に絞って計画を立案すればよく、ベテラン計画担当者がイメージしている内容を、スケジューラーに表現することが、ノウハウの見える化にもつながります。
また、精緻な時間でスケジューリングしても、製造現場ではその日時ピッタリに作業開始・終了することはできません。勤務時間や設備停止の状況を踏まえながら、最新オーダーを基に、どの設備でどの順序で作業をするのかを計画調整するという運用が、取り組みやすいと思います。製造業にも様々な業界の考え方がありますので、コルノットはユーザー様の工場の課題に向き合い、生産スケジューラーの活用について提案します。
自動スケジューリング
FLEXSCHEをはじめとする生産スケジューラーは機能が豊富なのですが、常に100点の自動スケジューリングをすることはできません。なぜなら、オーダーの状況が日々変動することはもちろんですが、計画担当者の考えも変わります。70点程度の自動スケジューリング結果から手調整することをお勧めします。そのためのスケジューリングルールの作成や、手調整の操作をしやすくするための画面設定およびアドインプログラムの開発をします。コルノットは日々使い続けることできる仕組みをインテグレーション(工場に馴染むように)します。
生産スケジューラー導入方法
コルノットでは生産スケジューラーFLEXSCHEの導入をプロトタイピング手法で行います。
短期サイクル(通常2週間)でプロトタイプの「検証⇒改良」を繰り返します。
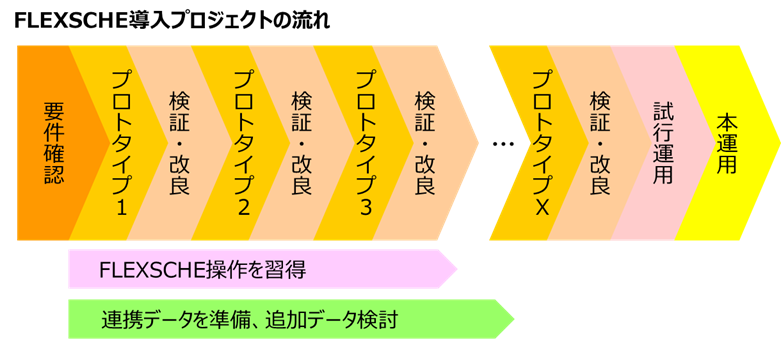
メリット
・早い段階でシステム完成イメージを共有できる
プロトタイプを確認・操作してみることで、システムのイメージを把握することができる。
・開発中の予期せぬリスクを回避できる
都度プロトタイプを確認するので「思っていたものと違った・・・」というトラブルを回避できる。
・システムの質を高められる
最初からシステム仕様が細かく決まっていることは稀である。都度アイデアを出しながら最終的な完成を迎えるため、システムの質を高めることができる。
デメリット
・導入プロジェクトが長期化するリスクがある
検証ごとに追加要求が多くなるケースがある。プロジェクト期間を意識して要求事項の整理を行う必要がある。
導入支援
コルノットはこれまで40社以上のFLEXSCHE導入経験があります。単なる技術支援ではなく、工場の課題解決のために生産スケジューラー導入および活用を支援します。導入費用やFLEXSCHEデモなど、お気軽にお問い合わせください。